
What about UHQCD?
For six years after the birth of HQCD, we continued to make trial-and-error efforts to reproduce audio at even higher quality. We researched new materials and investigated ways to reproduce audio with the highest possible fidelity. After a variety of experiments, we decided on a completely new approach to the task–radically changing the CD manufacturing process itself. We exhaustively questioned the conventional wisdom about CD manufacturing, which had remained largely unchanged across the world for over 30 years. Through this effort, which might seem ill-advised, we arrived at the ultimate in quality–a level of quality that is certainly impossible to achieve with existing CD discs.
Features of UHQCD
- Discs conform to the CD specification and are playable on existing Audio CD players.
- Master audio is reproduced more faithfully compared to existing high-quality CDs, thanks to a newly developed disc manufacturing process. Newly developed disc manufacturing process masks the sound quality of UHQ CD closer to the master quality compared to existing high-quality CDs
- Offers easy enjoyment of high-quality audio at a quality that is very close to that of Crystal Disc.
Conventional high-quality Audio CDs
We developed our conventional high-quality Audio CD discs through an effort to improve audio quality by simply upgrading the materials used in ordinary CD discs to higher quality materials. For example, for the substrate we used a high-transparency and high-fluidity polycarbonate (a type of plastic) of the type used for LCD panels, while for the reflective layer, we replaced low-cost, common aluminum with a unique and expensive alloy of high-reflectivity. These improvements made it possible for mass-produced CD discs to reproduce audio with greater precision. In fact, HQCD discs were used to release a wide range of classical and jazz music titles. The approach of upgrading raw materials is limited, however. To achieve further improvements in audio reproduction, we had to totally rethink the disc manufacturing process itself.
Differences in manufacturing methods
Conventional Audio CDs are produced using the technique of injection molding to form “pits” of data on polycarbonate material. Metal plate on which “pits” representing audio source data are formed is used as a die. This is called the “stamper.” Polycarbonate is melted at high temperature and poured into the die to duplicate the pit patterns on the stamper. This method is efficient because it enables high-speed production, but it does not enable totally accurate or complete duplication of the pits on the stamper. As a melted plastic, polycarbonate is inevitably viscous, so it cannot penetrate completely into every land and groove of the tiny pits of the stamper. We tried to reproduce finely detailed patterns using the high-quality polycarbonate used in LCD panels, but complete replication proved to be difficult. In the new method we developed, however, we used photopolymer instead of polycarbonate to replicate the pits of the stamper. In their normal state, photopolymers are liquids, but one of their characteristic properties is that they harden when exposed to light of certain wavelengths. Taking advantage of this property, we managed to achieve perfect replication of very finely detailed pits. Photopolymers in the liquid state are able to penetrate into the tiniest corners of pits on the stamper so that the pattern of the pits is reproduced to an extremely high level of accuracy. Like this, we successfully replicated and reproduced audio at a level that is impossible to achieve using conventional CD production technology.
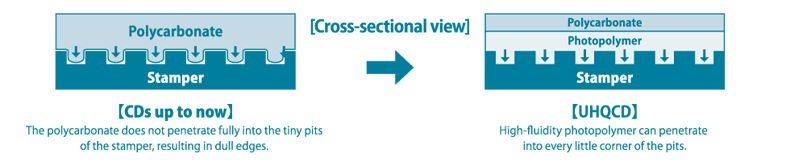
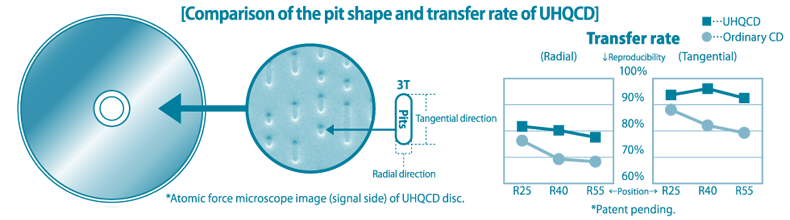
Although this CD manufacturing method is inherently less amenable to mass production than conventional method of CD production, after a great deal of time we managed to develop a way to mass-produce CDs with the new method. We hope you enjoy these totally “reborn” CDs.